Glass manufacturing is evolving, with advancements in technology driving efficiency and quality to new heights. A standout in this transformation is Elsisan's state-of-the-art spray coating lines, which redefine precision and efficiency in glass painting. In this blog post, we’ll explore what you need to know before purchasing a glass spray coating line, and how these systems operate. Since all customer requirements are unique regarding part details, paint specifications, and space limitations, these lines are custom-made for our customers’ specific needs.
Which Parts Can Be Painted in Our Glass Spray Coating Lines?
- Glass bottles
- Bottle closures
- Fragrance bottles and vials
- Plastic bottles
- Beverage bottles
And much more! Our systems are perfect for a wide range of products, and are not limited to the ones mentioned above.
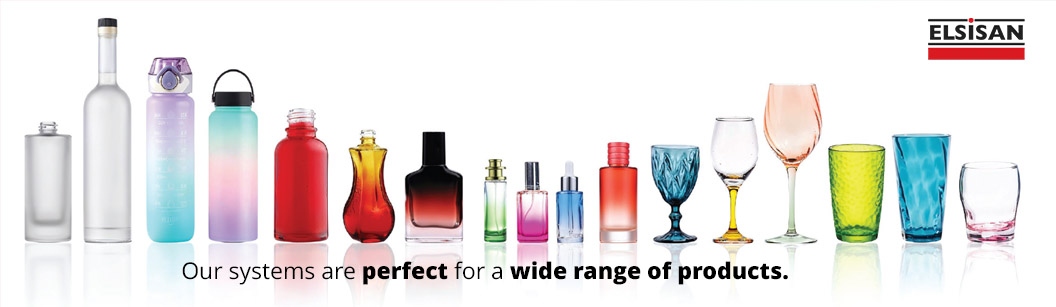
Things You Must Know Before Starting:
- Part Dimensions:
We need to know the minimum and maximum dimensions of your parts. This helps design the conveyor and the spacing of part holder jigs to enhance your efficiency. Part dimensions will determine several other factors as well, such as door openings, spray coating equipment placement, and painting booth dimensions. - Desired Capacity:
To accurately tailor your spray coating line for optimal performance, we need to specify your desired production capacity in units per hour. This will optimize your investment cost and line efficiency. Having a larger capacity than needed will result in inefficient and expensive line investment and operating costs. - Paint Technical Requirements (TDS Document):
It’s important to choose your paint chemicals before starting the design of your painting line. After you choose your paint, companies will provide a Paint Technical Data Sheet (TDS), which will provide information about specific requirements such as paint application environment requirements, flash-off and curing times, and requirements. If you haven't yet chosen your paint, the Elsisan team can recommend you a list of local and global companies who have expertise in this area to determine your paint chemicals and perform necessary laboratory tests. - Available Factory Area:
We need this information to determine the design of your machine. If there are any columns or obstructions in the area, or any other limitations in the space, we can work on different designs to solve and optimize your painting line design. It's also important to consider loading and unloading areas and parts stocking areas.
Sections of Glass Spray Coating Lines
After collecting the necessary information, we can start designing a spray coating line for glass. Let's look at the usual sections of such a line:
1. Loading Area
2. Pre-treatment: Flame Treatment
3. Pre-treatment: Anti-static Application
4. Paint Booth
5. Flashoff Area
6. Curing Oven Area
7. Cooling Area
8. Unloading Area
9. Control Panel
10. Electric Panel
11. Paint Kitchen
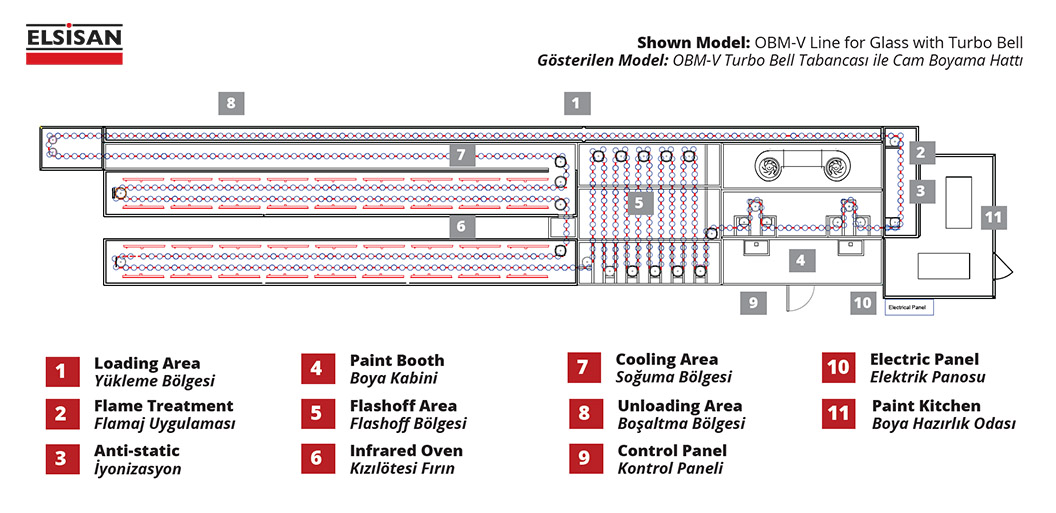
Loading Area
In the loading area, operators place the parts on top of part holding jigs which are specifically designed for customer’s parts. Some part holder jigs have different dimensions and masking areas to achieve customer’s requirements, so depending on the parts, the jigs may need to be changed. However, in most cases, universal part holder jigs can be designed to fit a variety of different products.
Pre-Treatment
In glass coating applications, pre-treatment is an important step to achieve desired quality and durability. Therefore, two main pre-treatment applications are applied to parts:
1.Flame Treatment:
Flame application cleans and increases surface tension for better paint adhesion on glass and plastic, ensuring a durable, high-quality finish.
2.Anti-static Application:
Antistatic bars are used to neutralize static electricity, effectively removing dust and improving the quality of the paint applied.
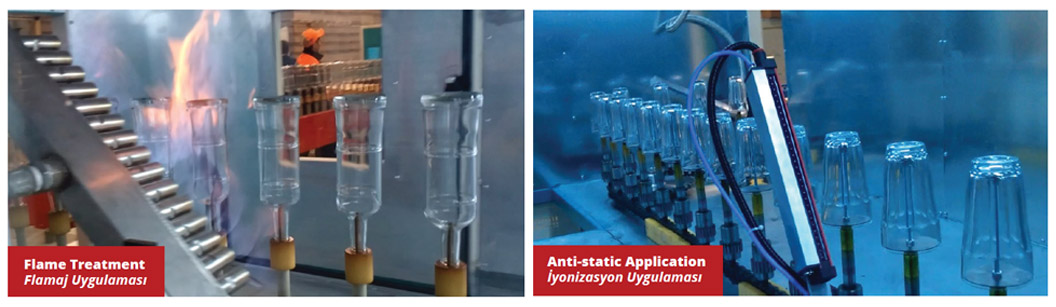
Paint Spray Booth
Inside the spray booth area, paint is applied through paint equipment in a controlled environment. Depending on the specifications of the Paint Technical Requirements, it’s highly important to create the necessary environment in terms of humidity and temperature to achieve the desired quality. As mentioned, there will be airflow inside the spray booth, and this airflow will help catch and filter overspray particles. There are two main options to catch overspray particles:
- Dry Filters:
Dry filters offer a cost-effective, space-saving option, capturing overspray particles with fibrous materials. - Water Screen:
Water screens, ideal for high-volume use, use a water curtain to trap and purify, with optional sludge separation systems.
Another vital aspect of spray booths is choosing the right equipment for your spray application to achieve desired effects and efficiency. Here’s what’s commonly used in spray glass coating applications:
- Conventional Air Spray Gun
- Electrostatic Spray Gun
- Electrostatic Turbo Disk (Rotary Disk
- Electrostatic Turbo Bell (Whirling Cup)
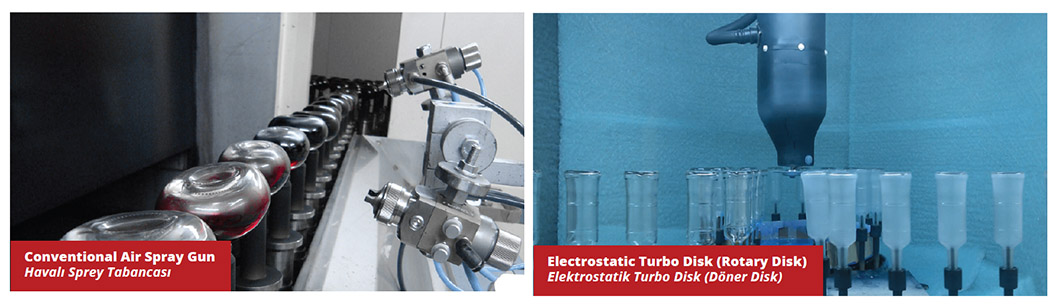
It’s also important for an operator to easily control and track the operations inside the spray painting booth, such as paint equipment stroke movements, filter changes, airflow, etc. That's why a touch panel will be located right outside the spray painting booth in a position where the operator can easily see inside the spray booth through glass and make necessary adjustments and controls. It will also securely log data for future reviews.
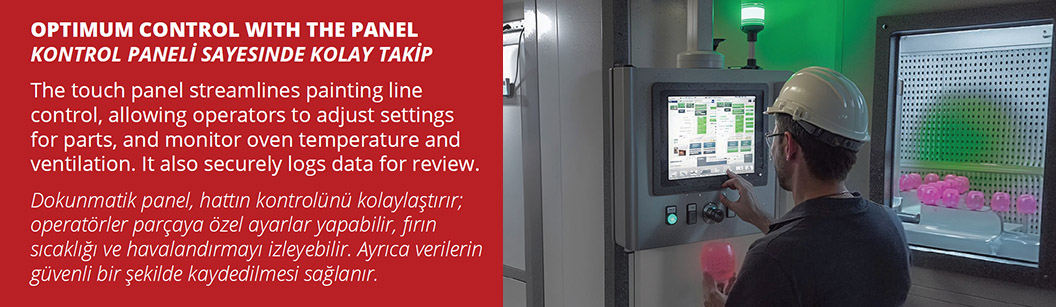
Flashoff Area
In the flashoff area, necessary exhaust and airflow will be created to achieve solvent evaporations. A certain amount of time needs to be spent in the flashoff area before the curing process can start.
Curing Area
In glass coating lines, the curing phase is crucial to achieve the desired quality and durability of the paint application process to meet industry standards. Depending on your paint type, there are certain curing methods which can be used, such as:
- Convectional Curing:
Conventional ovens offer versatility for various coatings, ensuring a uniform finish tailored to fit production needs. - Infrared Curing:
Infrared ovens ensure rapid, energy-efficient curing, ideal for high-speed production. - UV Curing:
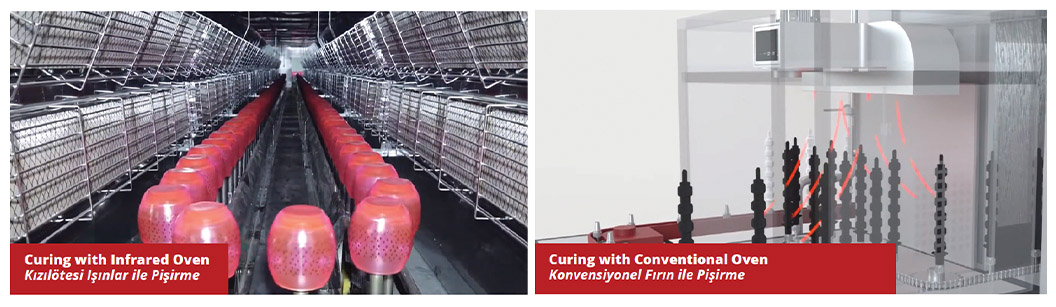
Cooling Area
After the curing area, depending on the curing method, there will be a certain amount of space reserved for parts cooling before an operator can unload the parts in the next section.
Unloading Area
In the unloading area, since the parts are cooled, operators can easily pick up and unload them. It's important to have enough space for stocking and boxing needs. While one operator can unload the parts, high-capacity lines may require more than one operator to quickly unload and move parts out of the conveyor area.
Customization and Additional Sections
As mentioned above, these are the main sections of most spray coating lines in the industry. However, more than one spray coating booth and curing areas may need to be added to the line to achieve certain effects or to work with different kinds of paint chemicals. When you contact our engineering team, we will guide you through your decisions, providing necessary advice to create efficient, long-lasting line operation details and help you choose the best investment strategy based on your parts, capacity, and other technical specifications.
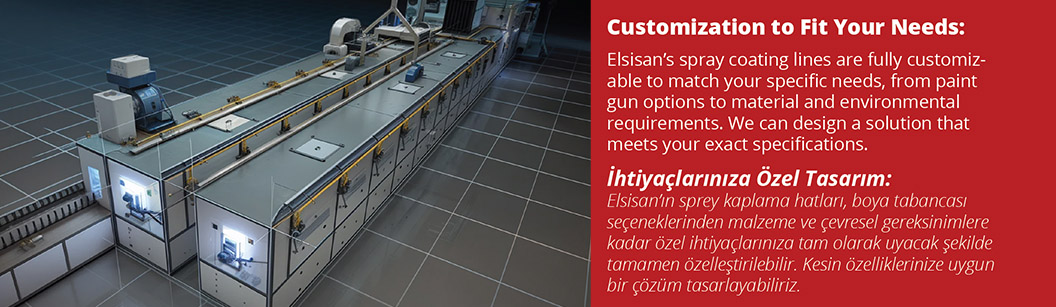
Elsisan's Comprehensive Services
- Engineering
Our engineering approach combines 3D visualization with expert analysis to identify challenges early and enhance efficiency, ensuring projects are effective from inception and adaptable to specific needs and environments. - Production and Installation
tilizing cutting-edge technology, we uphold high production standards. Transparent workflows keep clients informed, while modular designs and strategic installation methods ensure rapid, seamless integration into client operations. - Training
Our training programs are designed to empower clients, enabling optimal utilization of our systems. Through these programs, clients gain the necessary skills and knowledge for sustained success and maximum benefit from our solutions. - Service
Our dedication to clients extends beyond project completion. We offer global service and expert guidance. Using network connectivity, we remotely access machines for support, ensuring solution effectiveness and high client satisfaction.
Conclusion
At Elsisan, our motto is "From Concept to Completion: Engineering Your Success." We guide you along the way, providing necessary training and service even after the painting line is delivered. As a turnkey manufacturer of coating lines, we develop long-lasting relationships with our customers to be their global provider and partner in glass spray coating applications.
To learn more and get an offer, reach out to the Elsisan Team today through the email address and contact information below. We will be happy to assist you and provide our globally renowned lines to create the best investment strategy for your company.
Web : www.elsisan.com
E-Mail : elsisan@elsisan.com
- Log in to post comments