Innovative Glass Coating Lines for Industry Leaders: High Efficiency Spray Coating Lines
Elsisan introduces state-of-the-art spindle automatic coating lines, revolutionizing the glass painting process. Designed for precision and efficiency, our systems employ a chain-on-edge conveyance, seamlessly transporting glass objects through a series of coating applications. Each piece is securely mounted on rotating spindles, ensuring uniform coating distribution for a flawless finish. Our lines feature meticulously controlled spray coating stations, followed by advanced drying or curing zones to solidify the coating, ensuring durability and consistency.
A Quick Look at Our Chain on Edge Spray Coating Lines for Glasses
Watch this video for a quick look at the product's main features, technical options and usage details.
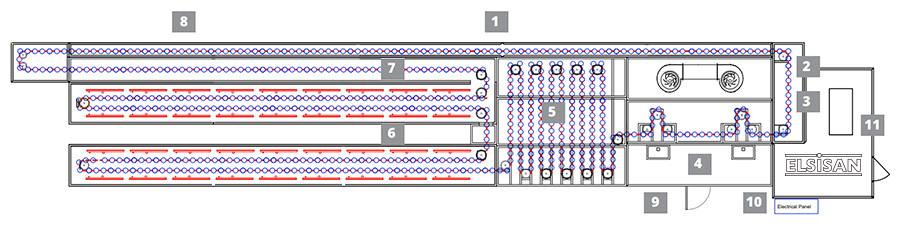
Our systems are perfectly suited for a wide and diverse range of products, including multiple industries, designed to meet the specific requirements of each product type.
- Glass bottles
- Bottle closures
- Fragrance bottles and vials
- Plastic Bottles
- Beverage Bottles
- And much more
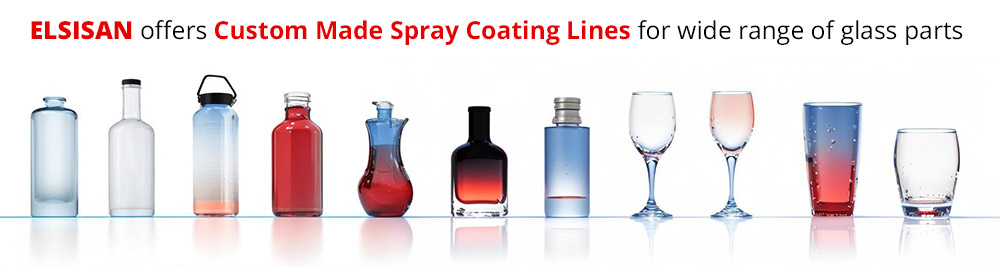
In glass coating applications, pretreatment is an important step. Antistatic bars are used to neutralize static electricity, effectively removing dust and thus improving the quality of the paint applied. Flame treatment application cleans and increases surface tension for better paint adhesion on glass and plastic, thus ensuring a durable, high-quality finish.
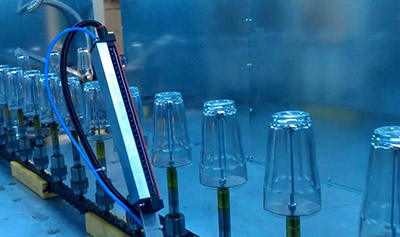
Ionisation/Anti-Static
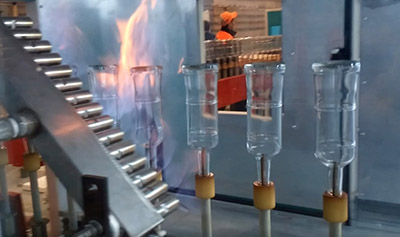
Flame Treatment
There are 4 main application types for spray glass coating applications.
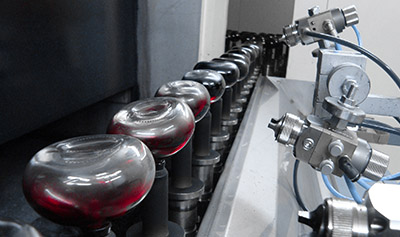
Conventional Spray Gun
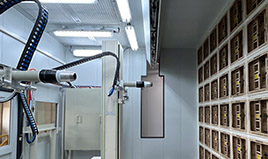
Electrostatic Spray Gun
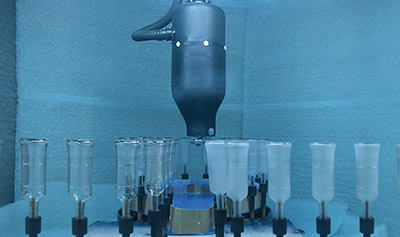
Electrostatic Turbo Disk (Rotary Disk)
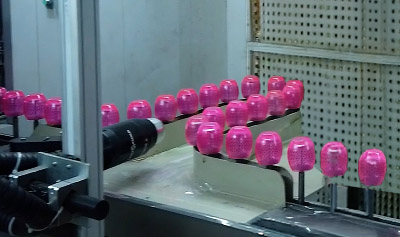
Electrostatic Turbo Bell (Whirling Cup)
We provide two filtering solutions for overspray paint: Dry Filter and Water Screen. Dry Filter offers a cost-effective, space-saving option capturing over-spray particles with fibrous materials. Water Screen, ideal for high-volume use, uses a water curtain to trap and purify, with optional sludge separation system.
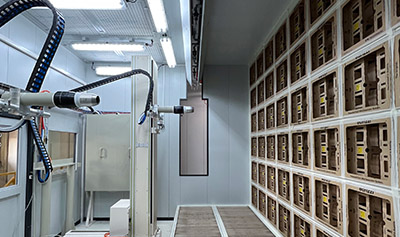
Dry Filter
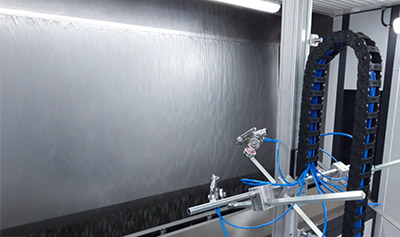
Water Screen
In our glass coating line, the curing phase is crucial, offering infrared or conventional ovens for curing. Infrared ovens ensure rapid, energy-efficient curing, ideal for high-speed production. Conventional ovens offer versatility for various coatings, ensuring a uniform finish. Tailored to fit production needs, both options enhance durability and quality of the coated glass, meeting diverse industry standards.
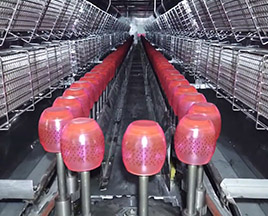
Infrared (IR) Curing
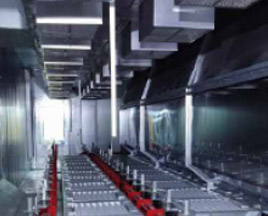
Convectional Curing
The touch panel streamlines painting line management, allowing easy adjustments of settings, temperature monitoring, and ventilation control. Its intuitive interface boosts productivity and precision. Secure data recording on the panel facilitates detailed analysis for enhanced process management and quality assurance, optimizing operations.
- Easy adjustments of settings, temperature monitoring, and ventilation control.
- Intuitive interface to boost productivity and precision.
- Secure data recording for detailed analysis.
- Enhanced process management and quality assurance.
Glass spray coating line for Perfume Bottles
Bottles spray coating line with Electrostatic Rotary Disk Application
Bottle spray coating line with Electrostatic Rotary Disk application
Spray coating line for Glasses with conventional gun and Electrostatic Turbo Bell
For the best-customized spray coating line for glass products, we need detailed information to ensure the system meets your needs and integrates seamlessly with your operations. Here's what we require:
Capacity
To accurately tailor your spray coating line for optimal performance, please specify your desired production capacity in units per hour.
Product Specs
Provide 2D drawings, photos, and if possible, 3D designs of your products to verify size and shape compatibility.
Paint Specs
Share the Paint Technical Data Sheet (TDS) for the chosen paint to adapt the line to specific flash-off times and curing processes.
Factory Layout
Detail the space allocated for the machine, including dimensions and any obstructions, for a custom fit.