In Dip Tank Lines, parts are loaded inside baskets and treated by dipping them inside each process tank for a prefixed period of time.
Iron phosphate and zinc phosphate surface treatment processes can be done in dipping lines. Materials are loaded into the material basket in the loading section. Select the appropriate program from the panel and press the start button. The carrier robot takes the basket in the loading area and places it in the first process tank. Baskets are kept inside treatment baths until the processing time is complete. When the process time is over, the robot automatically takes the basket and places it in the next process tank. The drying tank is the last tank to accelerate the drying of the materials coming out of the bath. When the drying time is up, the robot automatically leaves the basket in the unloading section. The parts are discharged from the basket or drum at the discharge zone.
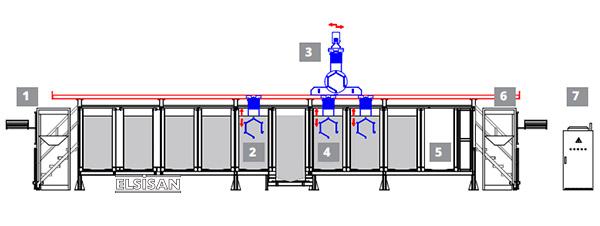
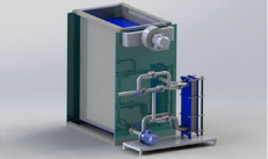
Tank Heating
Tank heating can be done by electricity, natural gas, hot water (plate or pipe type heat exchanger) and steam.
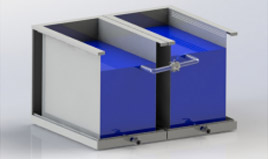
Reverse Cascade System
With the help of cascade system rinse water consumption is minimized.
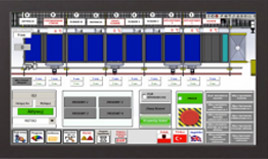
Control Panel
Parameters such as product recipes and tank temperatures in dip lines can be easily managed with the help of touch screen panels.
Customizaton to Fit Your Needs:
Elsisan's dip tank pretreatment lines are fully customizable to match your specific needs, from heating elements to material and process requirements. We can design a solution that meets your exact specifications.